PRODUCT CHANGE — Changes to Crimping on Select Nozzles
August 4, 2020
Effective immediately, you may notice a slight change to the crimp area of some Tregaskiss® nozzles. Within our manufacturing process, we have begun to transition from six-jaw to eight-jaw crimpers. Rest assured that the durability and performance of Tregaskiss nozzles will remain the same.
The only difference you will notice is a slight change limited to the crimp area of the nozzle. The difference is shown below:
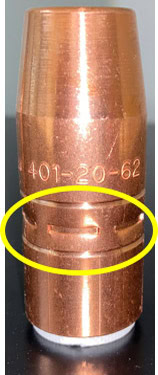

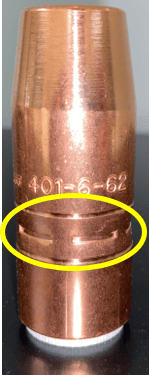

Timeline for Transitioning to Eight-Jaw Crimpers
(Actual ship dates will be dependent upon existing inventory levels at time of assembly transition)
- July 2020: This transition has already begun on part number 401-6-62, with additional part numbers to follow
- August 2020: All heavy duty (HD) Tregaskiss nozzles will transition to the new style crimp and will be completed by August 31
- September 2020: All standard duty (SD) Tregaskiss nozzles will transition to the new style crimp and will be completed by September 30
For complete product information:
AccuLock™ R Consumables
TOUGH LOCK® Consumables
DISCONTINUED PRODUCT – TOUGH GUN G2 and ThruArm G2 Series MIG Guns
DISCONTINUED PRODUCT –
TOUGH GUN G2 and ThruArm G2 Series Robotic Air-Cooled MIG Guns
December 1, 2017
As of December 29, 2017, all TOUGH GUN® G2 and ThruArm® G2 series robotic air-cooled MIG guns will be discontinued as they are being replaced by TOUGH GUN CA3 and TOUGH GUN TA3 robotic air-cooled MIG guns. The TOUGH GUN G2 and ThruArm G2 series product lines will be fully supported with replacement parts (necks, cables, gun modules) until the end of 2018.

Affected Part Numbers:
- All MIG gun part numbers beginning with RA2
- All MIG gun part numbers beginning with TA2
- All MIG gun part numbers beginning with SG59
Download PDF Archived Tech Guides:
- M074 TOUGH GUN G2 Series
- M080 TOUGH GUN ThruArm G2 Series
- M084 TOUGH GUN ThruArm G2 Series for FANUC® Robots
- M085 Technical Addendum for TOUGH GUN ThruArm G2 Series TOUGH GUN I.C.E.® Neck Installation for Motoman® Robots
Download PDF Archived Technical Inserts:
- INS070 Wire Brake Installation for TOUGH GUN G2 Series MIG Guns
- INS072 TOUGH GUN G2 Series TOUGH GUN I.C.E. Installation for KUKA® Robots
- INS091 TOUGH GUN ThruArm MIG Gun Installation
Download PDF Archived Configurator Spreads
- TOUGH GUN G2 Series MIG Gun Configurator Spread
- TOUGH GUN ThruArm G2 Series MIG Gun Configurator Spread
Tulsa Welding School’s Houston campus needs reliable equipment that can handle any process. Bernard® MIG guns and consumables are the answer. “Bernard (guns) they’re real comfortable in my hand you know. They’re not too big and bulky. They’re not too heavy. The neck ratio on that, is just, they’re awesome. I like them. The lighter the gun can be is great for a welder.”, Greg Langdon – welding instructor. “Here at Blinn when we chose welding equipment first and foremost I want something solid. That’s going to be there for me for years. In our labs we have connected all our Miller 22 A wire feeders to Bernard guns. Centerfire is so user friendly that I actually bought conversion kits and changed all our non-Bernard gear over to Bernard consumables” – Blinn welding instructor, John McGee. Instructors and students at Blinn College have come to rely on Bernard product for molding future welders. Bernard MIG guns and consumables are easy to use and a welder’s best choice in dependability.
Poor wire feeding is a common problem encountered in many welding operations. Unfortunately, it can be a significant source of downtime and lost productivity — not to mention cost. Poor or erratic wire feeding can lead to premature failure of consumables, burnbacks, bird-nesting and more. To simplify troubleshooting, it’s best to look for issues in the wire feeder first and move toward the front of the gun to the consumables. Finding the cause of the problem can sometimes be complicated, however, wire feeding issues often have simple solutions. When poor wire feeding occurs, it can be related to several components in the wire feeder. 1. If the drive rolls don’t move when you pull the trigger, check to see if the relay is broken. Contact your feeder manufacturer for assistance if you suspect this is the issue. A faulty control lead is another possible cause. You can test the control lead with a multimeter to determine if a new cable is needed. 2. An incorrectly installed guide tube and/or the wrong wire guide diameter may be the culprit. The guide tube sits between the power pin and the drive rolls to keep the wire feeding smoothly from the drive rolls into the gun. Always use the proper size guide tube, adjust the guides as close to the drive rolls as possible and eliminate any gaps in the wire path. 3. Look for poor connections if your MIG gun has an adapter that connects the gun to the feeder. Check the adapter with a multimeter and replace it if it’s malfunctioning. Using the wrong size or style of welding drive rolls can cause poor wire feeding. Here are some tips to avoid problems. 1. Always match the drive roll size to the wire diameter. 2. Inspect drive rolls every time you put a new spool of wire on the wire feeder. Replace as necessary. 3. Choose the style of drive roll based on the wire you are using. For example, smooth welding drive rolls are good for welding with solid wire, whereas U-shaped ones are better for tubular wires — flux-cored or metal-cored. 4. Set the proper drive roll tension so there is sufficient pressure on the welding wire to feed it through smoothly. Several issues with the welding liner can lead to erratic wire feeding, as well as burnbacks and bird-nesting. 1. Be sure the liner is trimmed to the correct length. When you install and trim the liner, lay the gun flat, making certain the cable is straight. Using a liner gauge is helpful. There are also consumable systems available with liners that don’t require measuring. They lock and concentrically align between the contact tip and power pin without fasteners. These systems provide error-proof liner replacement to eliminate wire feeding problems. 2. Using the wrong size welding liner for the welding wire often leads to wire feeding problems. Select a liner that is slightly larger than the diameter of the wire, as it allows the wire to feed smoothly. If the liner is too narrow, it will be difficult to feed, resulting in wire breakage or bird-nesting. 3. Debris buildup in the liner can impede wire feeding. It can result from using the wrong welding drive roll type, leading to wire shavings in the liner. Microarcing can also create small weld deposits inside the liner. Replace the welding liner when buildup results in erratic wire feeding. You can also blow compressed air through the cable to remove dirt and debris when you change over the liner. Welding consumables are a small part of the MIG gun, but they can affect wire feeding — particularly the contact tip. To avoid problems: 1. Visually inspect the contact tip for wear on a regular basis and replace as necessary. Look for signs of keyholing, which occurs when the bore in the contact tip becomes oblong over time due to the wire feeding through it. Also look for spatter buildup, as this can cause burnbacks and poor wire feeding. 2. Consider increasing or decreasing the size of contact tip you are using. Try going down one size first, which can help promote better control of the arc and better feeding. Poor wire feeding can be a frustrating occurrence in your welding operation — but it doesn’t have to slow you down for long. If you still experience problems after inspecting and making adjustments from the feeder forward, take a look at your MIG gun. It is best to use the shortest cable possible that can still get the job done. Shorter cables minimize coiling that could lead to wire feeding issues. Remember to keep the cable as straight as possible during welding, too. Combined with some solid troubleshooting skills, the right gun can keep you welding for longer.
November 11, 2019 In September 2017, Tregaskiss entered into a Master Distribution Agreement with DINSE GmbH to provide best-in-class robotic water-cooled MIG guns to the North American market under the Tregaskiss® by DINSE™ brand name. After many discussions between Tregaskiss and DINSE, we have made an amicable and mutual decision to end our business relationship. This notice is to officially announce that Tregaskiss will discontinue sales of Tregaskiss® by DINSE™ Robotic Water-Cooled MIG Guns, parts and consumables as of April 30, 2020. Until that termination date, Tregaskiss will not accept orders from new customers but will continue to provide product to support existing customers. Details of affected part numbers can be accessed here. When current Tregaskiss by DINSE Robotic Water-Cooled MIG Guns eventually require replacement, end users have two options: After April 30, 2020, please obtain all replacement parts and consumables from the relevant manufacturer. Please contact your local representative with any questions regarding these changes.
April 3, 2020 Tregaskiss is proud to announce the addition of two new nozzles to the AccuLock™ R consumables offering. Only slightly larger than 1/2″ bore nozzles, these 5/8″ bore nozzles offer almost the same weld access while still providing the clearance needed for reliable gas flow and reaming to the gas holes. These new nozzles are also now configurable on TOUGH GUN® TA3 and CA3 robotic air-cooled MIG guns. Learn more about AccuLock R consumables, or configure your robotic MIG gun online.
BEECHER, Ill. February 19, 2020 – Bernard has expanded its AccuLock™ S consumables system to include additional diffuser and nozzle types and sizes, as well as new contact tip options. The large AccuLock S consumables offering now features a new slip-on diffuser, along with a copper 3/8-inch bore tapered nozzle. Bernard has also added two new diffusers that allow small AccuLock S consumables to be installed easily, including thread-on and slip-on versions — plus compatible brass and copper nozzles with 5/8- and 1/2-inch bores and brass nozzles with 3/8-inch bores. A variety of tip recesses are available within the selection of nozzles. In the case of the small or large AccuLock S consumable offering, the same nozzle can install onto either a thread-on or slip-on diffuser. New tapered ‘TT’ series contact tips (0.350-inch O.D.) are available to accommodate wire diameters ranging from 0.023 to 1/16 inch and are compatible with both small and large AccuLock S diffusers and nozzles. The ‘TT’ series contact tips pair with tapered-profile nozzles to provide the same tip recess and better weld joint access. Like other contact tips in the system, the ‘TT’ series contact tips feature coarse threads that easily mate with the gas diffuser to reduce the risk of cross-threading and to speed replacement. The AccuLock S consumables, introduced in early 2019, were designed to reduce downtime, troubleshooting and rework associated with errors in liner trim length and erratic wire feeding. The system concentrically aligns the liner with the power pin and contact tip, locking it in place for a flawless wire feeding path. Welders don’t need to measure the liner during installation or replacement — they simply cut the liner flush with the back of the power pin for perfect liner trimming, every time. In addition to contact tips, nozzles and gas diffusers, the AccuLock S consumables require an AccuLock S-specific liner, power pin and power pin cap. # # #
February 14, 2020 Tregaskiss® and Bernard® branded nozzles are currently packaged in a variety of bag sizes and styles. We will begin standardizing on a single size and style bag for all Tregaskiss and Bernard nozzles over the coming months as a running change that takes place as existing inventory is depleted. 5″ x 8″ (white) 8″ x 10″ (white) 6″ x 8″ (clear) 8″ x 10″ (white) (subject to change depending on volume changes)
In many cases, equipment-based solutions can be a means to gain success in the robotic welding operation. They can mitigate costly risks and eliminate issues that lead to inefficiencies. And often, these issues are related to a small but significant part of the robotic welding process — the welding consumables. Changing over consumables can be a time-consuming part of maintaining the welding cell, especially if it is done multiple times during a shift. Changeover can also negatively impact productivity and quality if the consumables are installed incorrectly. Unfortunately, given the industry’s current lack of skilled welders, that may be a common occurrence. Welders simply have less experience with proper installation processes. To address this problem, many companies tend to spend more time and money on training and troubleshooting. They may even have to find workarounds to problems in the weld cell as employees get up to speed. All of this occupies resources. Welding consumables — the contact tip, gas diffuser and nozzle — can be a major source of downtime in robotic welding operations, unplanned or planned. During installation, cross-threading of contact tips by less experienced welders is a common occurrence that can result in unplanned downtime. Cross-threading leads to multiple problems beyond the lost productivity for contact tip changeover. First, it can negatively affect tool center point (TCP), causing the robot to weld off-seam and create quality issues like lack of fusion or poor penetration. Personnel overlooking the robotic welding cell then need to stop production to address rework and/or scrap the part. Cross-threading can also create a keyhole, or uneven wear, in the bore of the contact tip. A keyhole the size of only half the diameter of the wire can result in the robot welding off-seam. Many times, a cross-threaded contact tip will stick inside the welding gas diffuser. Without another gas diffuser readily available, the operator has to make a trip to the tool crib for a new one. Meanwhile the robot is offline and not producing parts. Plus, a company incurs costs for both the contact tip and the diffuser’s replacement. Companies that invest in power sources with a pulsed waveform capability — particularly in the automotive industry — often schedule planned downtime. Pulse waveforms improve productivity and quality by increasing travel speeds, providing a more consistent arc and reducing spatter. However, the pulsing action of the arc electrically and mechanically erodes the contact tip, leading to faster wear. It is necessary to plan downtime as a preemptive strike against contact tip failures before the chance of associated weld quality issues arise. Both unplanned and planned downtime cost money and occupy available labor for non-value-added activities — tasks that don’t support throughput and productivity. There is a new welding consumables technology that can help. To address the issue of cross-threaded contact tips, Tregaskiss designed its AccuLock™ R consumables. The design is intended to support higher throughput, provide a long service life and ensure good weld quality. The AccuLock contact tip features a long tail that concentrically aligns within the diffuser before the threads engage. The threads are also coarse, so they require minimal rotations to install. This design virtually eliminates the risk of cross-threading and provides three key benefits to the robotic welding operation: The contact tips also have greater mass at the front compared to other designs, along with a taper that mates securely with the gas diffuser. The tapered surfaces ensure optimal conductivity, reduce heat and keep the consumables locked in place. These features — combined with the fact that 60% of the contact tip is buried in the diffuser, away from the heat of the arc — make the consumables last longer. Extending the product life means there is less need for changeovers. AccuLock R consumables can also address the accelerated wear of contact tips caused by pulsed waveforms. In addition to offering the contact tips in copper and chrome zirconium, Tregaskiss has an AccuLock HDP option. The HDP contact tips last more than 10 times longer than copper tips in pulsed MIG welding applications. As a result, companies can reduce unplanned downtime for contact tip changeover — and make those changeovers faster because of the easy-to-install design. AccuLock R consumables can be implemented easily. Switching from many other consumables typically doesn’t affect TCP or robotic programming; however, it is best to consult directly with Tregaskiss to confirm this is the case. For companies that have both robotic welding and semi-automatic welding operations, the AccuLock R consumables can simplify complex inventories. The contact tips are part of a Common Consumable Platform™ and can be used across a wide range of Tregaskiss® robotic and fixed automatic MIG guns, as well as with Bernard® semi-automatic MIG guns (ranging from 200 to 600 amps). This common contact tip can reduce inventory costs and lessens the opportunity for operators to install the wrong consumable. The AccuLock R gas diffuser also has a blue o-ring to distinguish it from other diffusers. When companies find equipment solutions, like the AccuLock R consumables, that help reduce troubleshooting and downtime in their robotic welding operations, opportunities can increase. The ability to improve productivity and quality is at the forefront of those. But there may also be more time available to optimize the weld cell, make positive changes to workflow or material handling and seek out cost savings.In some cases, companies may also uncover issues in the weld cell that were previously masked by frequent contact tip changeovers. Now, however, there is more time address those to generate greater efficiencies in the operation. In short, with the right consumables, there is more time to focus on reaching improvement targets and increasing throughput — and on implementing training that can help achieve those goals.
For a cleaner, more compliant work environment, get right to the source and extract fumes at the weld with the Bernard Clean Air fume extraction gun. Build your ultimate MIG gun. Choose from a variety of necks, handles and trigger styles to optimize welder ergonomics and weld access. Then standardize with a single line of consumables to simplify maintenance and contain costs. You can count on Bernard BTB semi-automatic air-cooled MIG guns to deliver industrial-grade performance and reliability in the most demanding and abusive environments.
Now mobile friendly! Configure your Bernard semi-automatic MIG gun – anytime, anywhere.
Bernard AccuLock S consumables provide error-proof liner replacement every time — no measuring required! Dual-locked in the contact tip and power pin AccuLock S liners guarantees optimized wire-feeding. TOUGH GUN TA3 robotic air-cooled MIG guns are compatible with various through-arm style robots and provide outstanding precision and reliability. Configure to be the durable and reliable solution for best in class welding.
Engineered for hard tooling automation applications, Tregaskiss fixed automatic MIG guns are simple to maintain, durable and repeatable. They are available in air-cooled and water-cooled models.
High performance consumables with an armored neck and body plus simple internal connections equal Tregaskiss fixed automatic MIG guns. They are quick and easy to maintain for maximum up-time and throughput. Models available in air-cooled or water-cooled.
Automating spatter removal helps to extend the life of your robotic MIG welding guns and consumables. It can benefit your bottom line, production up-time and throughput. Choose between our TOUGH GUN TT4A reamer (analog model) or our new TOUGH GUN TT4E reamer (Ethernet model) for further enhanced with digital Ethernet communication for better integration.
Tregaskiss TOUGH GUN TT4 reamer is tough on spatter and operates reliably in even the harshest welding environments. Automating spatter removal will help to extend the life of your robotic MIG guns and consumables.
Designed for increased tip life, Tregaskiss AccuLock R consumables can reduce your replacement frequency and related planned downtime.
AccuLock HDP contact tips can increase life by an additional 6-10x or more in pulse welding applications.
Designed for increased tip life, Tregaskiss AccuLock R consumables can reduce your replacement frequency and related planned downtime. AccuLock HDP contact tips can increase life by an additional 10x or more in pulse welding applications.
Customize your Tregaskiss robotic MIG gun or reamer for your specific application using our new mobile-friendly online configurators!
Welding students in Tulsa benefit from Bernard MIG Guns and Consumables | Customer Testimonial
Welding students in Tulsa benefit from Bernard® MIG Guns and Consumables
Blinn Instructors Choose Bernard MIG Guns and Consumables for Dependable Welding Equipment | Customer Testimonial
Blinn Instructors Choose Bernard® MIG Guns and Consumables for Dependable Welding Equipment
How to Prevent Common Causes of Poor Welding Wire Feeding
How to Prevent Common Causes of Poor Welding Wire Feeding
What’s happening with the feeder?
Take a look at the drive rolls
is the wrong size for the wire being used.Check the liner
Monitor for contact tip wear
Additional thoughts
DISCONTINUED PRODUCT – Tregaskiss by DINSE Robotic Water-Cooled MIG Guns
DISCONTINUED PRODUCTS –
Tregaskiss by DINSE Robotic Water-Cooled MIG GunsReplacement MIG Gun Options
Parts and Consumables
NEW PRODUCT – Tregaskiss Nozzles for AccuLock R Consumables
NEW PRODUCT —
Tregaskiss Nozzles for AccuLock R ConsumablesPart Numbers
Bernard Expands AccuLock S Consumables Offering
Bernard Expands AccuLock S Consumables System
PACKAGING CHANGE – Changes to Tregaskiss and Bernard Nozzle Bag Packaging
PACKAGING CHANGE –
Changes to Tregaskiss and Bernard Nozzle Bag Packaging
Current Bag Sizes and Styles:
New Bag Size and Style:
Transition Timeline
AccuLock R Consumables Reduce Downtime in Robotic Welding
AccuLock R Consumables Reduce Downtime in Robotic Welding
Consumable challenges
A new consumables solution
Making the change
Bernard Clean Air Fume Extraction MIG Welding Guns
Bernard® Clean Air™ Fume Extraction MIG Welding Guns
Bernard BTB Semi-Automatic Air-Cooled MIG Welding Guns
Bernard® BTB Semi-Automatic Air-Cooled MIG Welding Guns
Video | Configure your Bernard Semi-Automatic MIG Gun Online
Configure your Bernard® Semi-Automatic MIG Gun Online
Bernard AccuLock S Consumables No Measuring Required
Bernard® AccuLock™ S Consumables – No Measuring Required
Bernard AccuLock S Consumables Dual-Locked Liner
Bernard® AccuLock™ S Consumables: Dual-Locked Liner
TOUGH GUN TA3 Robotic Air-Cooled MIG Welding Guns
Tregaskiss® TOUGH GUN® TA3 Robotic Air-Cooled MIG Welding Guns
Tregaskiss Fixed Automatic MIG Guns
Tregaskiss® Fixed Automatic MIG Guns
Video | Tregaskiss Fixed Automatic MIG Guns
Tregaskiss® Fixed Automatic MIG Guns
Tregaskiss TOUGH GUN Reamer Robotic Nozzle Cleaning Stations
Tregaskiss® TOUGH GUN® Reamer Robotic Nozzle Cleaning Stations
Video | Tregaskiss TOUGH GUN Reamer Robotic Nozzle Cleaning Stations
Tregaskiss® TOUGH GUN® Reamer Robotic Nozzle Cleaning Stations
Video | Tregaskiss AccuLock R Consumables for Better Throughput
Tregaskiss® AccuLock™ R Consumables for Better Throughput
Video | Tregaskiss AccuLock HDP Contact Tips
Tregaskiss® AccuLock™ HDP Contact Tips
Tregaskiss AccuLock R Consumables
Tregaskiss® AccuLock™ R Consumables
Video | Configure your Tregaskiss Robotic MIG Gun and Reamer Online
Configure your Tregaskiss® Robotic MIG Gun and Reamer Online