Maintaining Your MIG Gun… and Your Welding Costs
Selecting the right MIG gun for your welding application, and maintaining it properly, is just as important to your overall productivity as any other part of the welding operation. Unfortunately, MIG guns are very often an overlooked part of the welding system. The reality is, however, that in addition to being responsible for delivering the current, wire and shielding gas to the weld puddle, your MIG gun can also have a significant impact on your weld quality and your bottom line.

Similar to selecting your power source or wire feeder, the goal is to find the most cost-effective MIG gun that is capable of providing you with the performance that you need for your welding application. Regularly executing preventive maintenance can then help you protect that investment.
Here are some tips to help you select the right MIG gun for your application and maintain it properly.
Choose the Right MIG Gun for Your Application
We all have the tendency to fall victim to the “bigger is better” philosophy. When it comes to purchasing a MIG gun, however, that thinking may cost you more money than is necessary for this equipment. It can also lead to costly downtime.
It is a common misconception that a welding procedure requiring 400 amps, for example, also requires a 400-amp MIG gun capable of operating at those amperage levels 100 percent of the time (i.e., 100 percent duty cycle). The fact is you spend time moving parts, grinding, tacking and completing other such tasks as opposed to welding nonstop. That means that you can often purchase a smaller amperage MIG gun for applications in which duty cycle is less than 100 percent for less money and still have it operate at the appropriate capacity. In this case, 300-amp model would suffice.
A smaller, lower-amperage MIG gun also weighs less and can help reduce wrist fatigue that could lead to downtime. It offers the added benefit of being easier to maneuver, which can help improve weld quality, too, and lessen rework.
When possible, using shorter power cables on your MIG gun can further minimize costs and downtime. As a general rule, shorter power cables are less expensive and, like a smaller MIG gun, offer better maneuverability. Shorter power cables also help minimize wire-feeding problems associated with kinking and coiling, so you can spend more time welding and less time resolving these issues.
Other factors you should consider when selecting your MIG gun:
- Select guns with a rigid strain relief (the connection between the power cable and power pin). A good strain relief helps minimize kinking that can lead to poor wire feeding, an unstable arc and poor weld quality.
- Select a trigger that is comfortable and easy to service. MIG guns are available with a variety of trigger options (e.g., standard, locking, dual schedule, etc.) and you may find that you prefer one over the others. Also, look for sturdy triggers that will withstand work site abuse and that can be easily replaced should one of the mechanics fail. Doing so can minimize downtime for maintenance and repairs.
- Find the right neck for your application. Typically, MIG gun manufacturers offer fixed, rotating and flexible necks in various lengths and angles. Having the right one for your application makes it easier to reach the joints that you need to weld and can help you get your repairs done more quickly and easily. Look for a neck with good armor to protect it against damage that could lead to electrical shorts or premature failure.
Consider using the smallest handle that can still meet your amperage needs. As with a smaller gun, smaller handles are easier to maneuver and can lessen fatigue. Some manufacturers also offer ventilated handles that help reduce heat and make it more comfortable to use for longer periods of time.
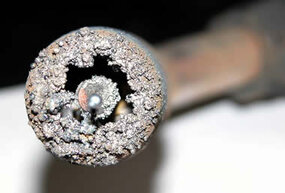
Maintaining Your MIG Gun
Regularly inspecting your MIG gun can be an important part of reducing costs and gaining good welding performance. Fortunately, preventive maintenance (PM) for a MIG gun doesn’t have to be time consuming or difficult. Consider these key factors.
Check the feeder connection
Regularly check the wire feeder connection (where the power pin plugs into the feeder) to be certain it is tightened properly and that there is no dirt or debris on it. Loose or dirty wire feeder connections can cause heat to build up, leading to voltage drops that adversely affect the welding arc and may cause premature gun failure. Tighten the connection according to the manufacturer’s specifications or replace the direct plug if necessary to obtain a secure fit. Also inspect the O-rings for cracks that could lead to gas leaks, and replace them as necessary. Gas leaks often cause spatter and porosity, which increases downtime for cleanup and rework.
Properly care for your MIG gun liner
It is not uncommon during the course of welding for the MIG gun liner to become clogged with debris, particularly from the welding wire. Over time, this accumulation of debris can lead to poor wire feeding, bird-nesting and burnbacks that require downtime to rectify. To maintain your liner, you can use compressed air to clear out potential blockages when you change wires. Also, tracking the length of time it takes for your liner to wear can help you better know when to replace the next one before you encounter problems. Always follow the manufacturer’s recommendation for trimming and installing the liner to prevent kinking and wire-feeding problems.
Inspect the handle and trigger
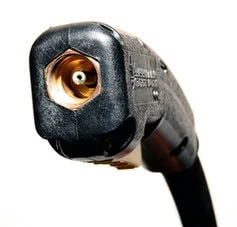
Typically these components require little maintenance beyond visual inspection. Regularly look for cracks on the handle or
missing screws. Check that your MIG gun trigger is not sticking or otherwise malfunctioning. Replace these components as necessary.
Check the MIG gun neck
Loose connections at either end of the neck can cause electrical resistance that leads to poor weld quality and/or consumable failures. Check regularly to ensure tight neck connections. Also, visually inspect the insulators on your MIG gun neck and replace if damaged. These insulators prevent electrically live components from exposure, ensuring your safety and the longevity of your equipment.
Visually inspect the power cable
Power cable maintenance is a very important part of eliminating unnecessary equipment costs. Regularly inspect the power cable for damage, including cuts or kinks, and replace it as necessary. Cuts in the cable can expose copper wire and lead to a potential shock hazard, while kinking obstructs gas flow and wire feeding. The latter can lead to weld defects and arc instability that require downtime to remedy.
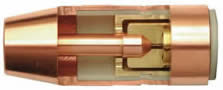
Be mindful of your consumables
Frequently inspect your MIG gun nozzle and contact tip for signs of spatter build-up, which can obstruct shielding gas flow and cause weld defects that will need to be reworked. Spatter build-up can also cause your consumables to fail prematurely. Replace both consumables if spatter build-up appears or clean according to the manufacturer’s recommendation. Also, be certain that these components (and the gas diffuser) are securely connected. Loose connections can increase electrical resistance, which in turn leads to poor welding performance and can shorten the life of your consumables, adding to your overall costs.
Remember, just like the power source and wire feeder, your MIG gun can impact your weld quality, productivity and costs. Taking the time to select the proper MIG gun and maintain it regularly, however, can help this equipment last longer and ensure that you spend more time welding instead of resolving problems.
From the power source to the welding wire, each of the components in an arc welding operation can have a significant impact on productivity. The welding gun and consumables — nozzles, contact tips and diffusers — in particular, are often an overlooked aspect of the whole process, but these components directly affect quality, welder comfort, rework, downtime and more. There are three key ways in which guns and consumables used in flux cored arc welding (FCAW) and gas metal arc welding (GMAW) can lead to improved productivity: The contact tip is the last point of contact between the welding equipment and the welding wire, as well as the consumable responsible for generating the electrical connection to create the arc. As the wire passes through the contact tip, it can often erode the inside of the tip bore, leading to interruptions in the electrical current and causing poor arc stability. During the normal course of welding, especially at higher amperages, the contact tip can also become loose and cause a burnback (or the formation of a weld inside the contact tip). Burnbacks are often a significant source of downtime in a welding operation — and a big hindrance to productivity. Having a contact tip that stays securely placed during the course of welding is key to combating burnbacks. Brooklyn Iron Works (Spokane, Wash.) found just such a solution when they converted to Centerfire™ contact tips last year. Like other structural fabrication companies, Brooklyn Iron Works faces stringent deadlines for its projects, so the ability to minimize downtime for burnbacks and any other equipment management is imperative. Their welding personnel run their weld beads at high amperages (300 to 400 amps) using typically .052- or 1/16-inch FCAW wire diameters, which often proved too harsh on their previous contact tips. They would loosen after routine welding, causing the wires to arc back and create the burnback. “Before we converted to the new contact tips, we had a substantial amount of downtime for contact tip changeover,” explains QA Manager, Phil Zammit. “And that’s money. It’s lost arc time for tip maintenance. Now we are using a third fewer tips and don’t have to worry about the downtime like before.” The company’s new contact tips don’t loosen because they “drop in” the diffuser and are locked in place by tightening the nozzle. They also feature a non-threaded tip design with a tapered base and large diameter seat. The other benefit of the design is that it helps generate consistent electrical conductivity and heat transfer, both of which help the consumables last longer and perform more reliably. Brooklyn Iron Works’ welding operators frequently encounter weld joints up to 2-in. deep. In the past, they often had to extend their electrode stickout as far as 2 inches to access the joints, a practice that risked generating porosity since it could compromise the necessary shielding gas coverage. Brooklyn Iron Works has found their solution to porosity is to have the right size and shape of nozzle for the application. Switching to Centerfire consumables now allows them to reduce electrode stick-out and gain better gas coverage at the same time. “These consumables direct the gas exactly where we need it,” Zammit explains. “It keeps our gas shielding coverage right at the weld, even when the doors are open or we have a breeze. We’ve never had a huge problem with porosity, but now we have even less of one.” The nozzles feature a tapered shape that stays fixed flush with the contact tip. They also include a built-in spatter shield that acts as an additional gas diffuser and ensures a more consistent directional gas flow, even on deep joints or if there is a slight breeze present. The typical welding operator spends time during a shift allocated to joint preparation, part fit-up and movement, along with other activities that contribute to the throughput of the welding operation. But during the actual process of welding, it is critical that he or she remain comfortable. Good welding operator comfort lessens the chances of injuries associated with repetitive movement and reduces overall operator fatigue. And a more content employee also brings forth the potential for greater productivity. Welding operators at Brooklyn Iron Works have addressed the issue of comfort through the various necks available on their Bernard 400-amp Q-Guns. The Q-Guns are available with fixed, rotatable and flexible necks in various lengths and bend angles. These neck options help the welding operators better accommodate the varying welding angles they encounter on projects. They can reach the weld joints better and minimize downtime to address issues like wrist fatigue. The flexible necks are especially helpful on difficult joints, as they can be adjusted to weld around corners or to fit into complex shaped steel components. Welding operator Ricky Curtis explains, “I can bend the neck in any direction I need. Even around the corners. I like that the gun does the work for me, instead of my wrist.” According to the company’s maintenance supervisor, John Dahl, there have been additional benefits to the design of the gun as well. “It takes only about five minutes to change a neck on these guns, compared to nearly an hour with our previous guns,” he explains. This ease of maintenance is another way in which having the equipment has helped Brooklyn Iron Works reduce downtime and get back to welding faster. Remember, in the long run, companies can benefit from looking at how every aspect of their welding operation impacts downtime. Time spent for changing out contact tips or maneuvering unnecessarily into difficult joints can ultimately hinder productivity, as can having welding guns that are time-consuming to maintain. Addressing the problem of productivity may be as simple as looking at a new consumable option or finding ways to make the welding operators more comfortable.
Gas metal arc welding (GMAW) involves more than just arc-on time. Welding operators also need to be mindful of other activities that contribute to the overall productivity and quality in the welding operation, including proper joint preparation, following correct weld parameters and ensuring good part fit-up. Selecting the proper GMAW gun, consumables and shielding gas is also critical to achieving good results. Unfortunately, it is not uncommon for there to be confusion as to how these components affect the welding operation. The reality is, however, that they can have a significant impact on downtime and costs, not to mention operator comfort. The goal is to make sure that impact is positive. Following are answers to some common questions about GMAW guns, consumables and shielding gas to help you select the best ones for your welding operation and manage them in a way that provides optimal results. When it comes to GMAW guns, bigger isn’t always better. In fact, selecting a larger amperage gun than needed for your application may cost you money in the long run and lead to discomfort, which results in unnecessary downtime. Duty cycle is defined as the amount of arc-on time within a 10-minute period, so a 20 percent duty cycle would constitute two minutes of arc-on time in a 10-minute time frame. Because most welding operators don’t weld 100 percent of the time, it is often possible to use a lower amperage gun for a welding procedure that calls for a higher amperage one. For example, in many cases you could use a 300-amp gun model in place of a 400-amp gun model, since actual arc-on time often does not exceed the amperage to duty cycle ratio of a 300-amp gun. The benefit is that the lower amperage gun generally costs less money — and it also weighs less, which can help reduce wrist fatigue, commonly associated with downtime. The lower amperage GMAW gun will still be capable of operating at the appropriate capacity, while also offering the benefit of being easier to maneuver – a factor than may help you improve weld quality and lessen rework, too. There are several factors to consider when choosing your GMAW gun. After determining your amperage needs, you should also look for features like a rigid, strong strain relief. Strength in this area between the power pin and cable can help minimize kinking, which often leads to an unstable arc and/or poor wire feeding. Next, consider selecting a smaller handle gun (but one that can still meet your amperage needs), as it may help reduce wrist fatigue and be easier to maneuver into complex joints. You may also want to consider looking for a specific style of neck for your application. Many GMAW gun manufacturers offer fixed, rotating and flexible necks in various lengths and angles, allowing you to reach joints more easily. Regardless of the style of neck you choose, you should find one with good armor to protect it against damage that could lead to electrical shorts or premature failure. Finally, select a GMAW gun with a comfortable and easy-to-service trigger. Typically, you will be able to find a variety of trigger options, including standard style, locking or dual schedule. Regardless of the specific style, look for sturdy triggers that will withstand work site abuse and that can be easily replaced should one of the mechanics fail. Shielding gas prevents exposure of the molten weld pool to oxygen, nitrogen and hydrogen contained in the air atmosphere, in order to protect the weld from contamination and/or defects. The type you use can impact everything from the penetration profile to arc stability and the mechanical properties of the finished weld. If you need deep weld penetration, particularly on thick materials, carbon dioxide (CO2) is a good choice and it is also the least expensive. This gas, however, does tend to create spatter and is limited to use in short circuit welding. Adding 75 to 95 percent argon to the CO2 can provide better arc stability and puddle control, both of which reduce spatter compared to straight CO2. This mixture will also allow you to use a spray transfer process, allowing you to weld faster in many cases. Argon also produces a narrower penetration profile that is useful for fillet and butt welds. If you’re welding a non-ferrous metal — aluminum, magnesium or titanium — you’ll need to use 100 percent argon. In some cases, oxygen or helium is used in the GMAW process, but it is not as common. Consumable service life can vary dramatically from application to application. There are a few steps you can take to make them last longer, however. First, use the correct contact tip for the size wire who have and be certain it fits securely with the gas diffuser. A solid connection between these components helps ensure good conductivity and minimize overheating, making them last longer. Also, inspect your nozzle on a regular basis for spatter and clean as necessary. Use a pair of welding pliers or a special nozzle-cleaning tool for the job, as directed by the consumable manufacturer. Be sure, too, that you have the appropriate type of consumables for your application. Applications above 300 amps, for instance, can often benefit from heavy-duty consumables, which have greater mass and can dissipate heat more readily. The result, in many cases, is longer service life. Finally, set the drive roll tension on your wire feeder so that the wire feeds properly. Doing so prevents deformities in the wire (in the case of too high of tension) that may cause the wire to wear out the contact tip prematurely. Cutting a GMAW liner too long can cause it to become misaligned with the gas diffuser. Conversely, cutting a liner too short may lead to debris build-up between the liner and gas diffuser. Both instances can lead to poor wire feeding, weld quality issues and premature contact tip failure. To prevent this problem, always follow the manufacturer’s instructions for installation, making certain that the liner is free of any burrs or short edges after you trim it. A smooth cut helps ensure smooth and consistent feeding of the welding wire. Some manufacturers offer a liner gauge to help you determine the proper length for your particular liner, while others print markings on the outside of the weld cable to show when the liner is twisted, allowing for more accurate trimming. If your gun does not have these markings, make sure the cable is fully extended when inserting the new liner. Remember to wear gloves when handling the liner and avoid dragging it on the ground. These precautions help prevent debris from being introduced into the GMAW gun and causing weld contamination and/or poor consumable performance. Burnback is one of the most common causes of downtime in a GMAW application and is a significant cause of premature contact tip failure. Proper equipment setup is one of the key defenses to protect your consumables. First, be sure that you have established the appropriate contact tip recess and wire stick out for your application, and that you maintain a correct contact-tip-to-work distance. Check electrical connections regularly and replace worn work leads or cables, as faulty ones can also cause the problem. Make sure to maintain the proper drive roll tension and install your liner properly, too. Both precautions minimize erratic wire feeding that could lead to burnbacks. Storing and handling GMAW consumables properly not only helps them last longer, but also perform better. Never store your GMAW consumables loose in a bin, since it can cause scratches on them that attract spatter and may lead to premature failure. Instead, keep them in their original packaging until you are ready to use them. Doing so will also protect the components from contaminants such as dirt or oil. Finally, always wear clean gloves when handling or replacing contact tips, nozzles and diffusers. Again, it helps prevent dirt, oil or other contaminants from adhering to them and also potentially entering the weld puddle. Like any welding process, GMAW has many factors to consider in order to achieve the best results. Make sure that you don’t overlook the impact of your GMAW gun, consumables and shielding gas as part of those. Being mindful of the selection process, storage and handling, and installation, among other things, can be beneficial to both your productivity and your bottom line in the long run.
Owner of Jolson Welding, Bob Jolson, talks about how Bernard’s Q-Gun MIG gun has increased his productivity and reduced his back pain while welding large diameter pipe. “You can go online and build a gun and they’ll send it right to you with everything you want to your spec. I’ve got a flexible gooseneck. They make them in a six and eight inch size, which is really a major asset because we get into lots of tight places and tight spots” Bob Jolson, owner of Jolson Welding, talks about the benefits of Bernard’s Centerfire consumables – “we get probably three to four more times their lifetimes on the tip and they basically they don’t wear out. I used to carry a baggie of them in my pocket. Now the same one goes to the washing machine two or three days in a row. I still get it back and keep it in my pocket” Owner of Jolson Welding, Bob Jolson, talks about the advantages of Bernard products in his welding operation. He discusses his favorite part of the Bernard Q-Gun™ semi-automatic air-cooled MIG gun. “When I got with Bernard products and had this Q-gun made up for me with a flexible gooseneck. Which is really a major asset because we get into lots of tight places and tight spots. It’s really nice.” Bob’s love for the Dura-Flux™ self-shielded flux-cored gun is very simple. “The reason why I like the Dura-Flux gun most important of all, I think, is the micro switch inside the trigger. I also like the little trigger guard here. My competitor’s gun they had this big old thing heat shield and basically it’s always in your way” “As far as the tip wear goes like I was saying we get probably three to four more times or lifetimes on the tip and they basically they don’t wear out” Centerfire™ consumables has helped gain productivity for Jolson Welding. Tico Terminal Trucks & Trailers improved productivity and reduced welding costs using Bernard Q-Gun™ semi-automatic air-cooled MIG guns and Centerfire™ consumables. “We had an opportunity through one of our suppliers to test the Bernard Centerfire tip system and initially I provided that system to my best welder in house I felt like he would be the one person that could tell me honestly if it was a valuable product to us or not. Within two weeks his only response was – “I love it”. Weld quality has improved and it is simply because we get a more accurate flow of gas on the weld. The huge advantage to the Centerfire tip system is the fact that it’s not a threaded in tip. So when you do in fact arc out a tip, it doesn’t require a lot of time to remove the tip put in a new one. They’re also much more durable, so that happens a lot less.”Three Ways Welding Guns and Consumables Can Improve Productivity
Three Ways Welding Guns and Consumables Can Improve Productivity
Contact Tips
Better Shielding
In addition to inadequate shielding gas, porosity can also occur if a welding operator uses too small of a nozzle for the application, extends the welding wire too far beyond the end of the nozzle or tries to weld with a nozzle full of spatter. Air from outside or from fans can create the problem, too, by blowing away much needed shielding gas.The Benefits of Comfort
GMAW Guns, Consumables and More – Common Questions Answered
GMAW Guns, Consumables and More: Common Questions Answered
How do I determine what amperage GMAW gun I need
Besides amperage, what else should I consider when selecting a GMAW gun?
What type of shielding gas is best for my application?
How can I make my GMAW consumables last longer?
What is the proper way to trim and install my GMAW gun liner?
How can I protect my contact tips from burnback?
What’s the best way to store and handle my GMAW consumables?
Increase productivity: MIG Welding with a Bernard Q-Gun MIG Gun | Customer Testimonial
Increase productivity: MIG Welding with a Bernard® Q-Gun™ MIG Gun
Gain productivity in MIG Welding with Bernard Centerfire Consumables | Customer Testimonial
Gain productivity in MIG Welding with Bernard® Centerfire™ Consumables
Jolson Welding discuss advantages of Bernard MIG guns, flux-cored guns and consumables | Customer Testimonial
Jolson Welding discuss advantages of Bernard® MIG guns, flux-cored guns and consumables
More Productivity and Lower Costs: Tico Adopts Bernard® MIG Welding Guns & Consumables | Customer Testimonial
More Productivity and Lower Costs: Tico Adopts Bernard® MIG Welding Guns & Consumables